Plastic injection molding and prototype injection molding are not exactly new. While it’s true that the latter came to be about three decades ago, the first one has been around for more than a century. It’s one of the manufacturing techniques that have changed the way the world works, and it’s still evolving. Inside the many topics regarding this ever-evolving tech, there is a discussion about the options of using hot runner and cold runner systems.
A runner system is a channel that can take the flow of melted plastic from one point to another to fill the cavities of mold. The first thing we need to understand in this regard is the fact that there is no better or worse option when it comes to these runners. As manufacturers, it is essential to understand the fundamental differences between these technologies. With the knowledge at your hand, you will be able to discuss further options of manufacturing with your clients, given their specifications on any given project.
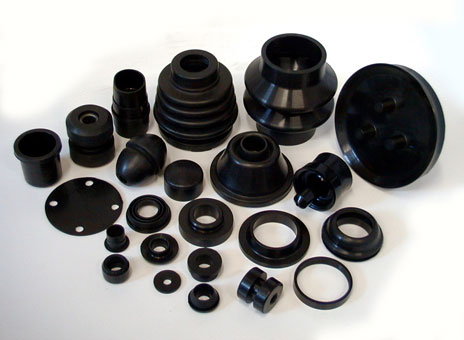
prototype injection molding components*
prototype injection molding components is from https://www.rpmindinc.com
Cold Runner Molds – How They Work, What They Do
A cold runner mold is formed by two or three plates that are held in place within the mold base. The molten resins are injected on the mold using a nozzle through a sprue. The sprue will fill all the runners that are directed at the mold cavities. As we use this system, we will notice that the runners are not heated and the work as a delivery system to distributes the molten plastic to each molding cavity. The cold runner system cools the sprue, the runner, and the gate as well as the molded part.
If we are working with two-plate molds, the sprues and the runner system will be attached to the finished product. An ejection system will be used to get the molded component out of the core half of the mold. When we deal with three-plate molds, a bare plate holds the sprue to deliver the molten resins to the set of runners that are contained on separate cavity plates. The finished molded part is created and cooled inside the core half of the plate with no runners or gates attached. This system separates the runner automatically from the part after the mold gets open.
In both systems, the runner can be reground and recycled to avoid plastic waste.
Hot Runner Molds – How They Work, What They Do
Injection molding projects handled using hot runner molds use two plates that are heated using a manifold system. This manifold is in place to help keep a consistent temperature in the runners holding the molten resins, as they go from their heating cylinders to the nozzles that will deliver the melted plastic and fill the core mold and create a product. The heated runner system is handled in a separate plate that remains in place during the molding cycle. After the procedure is done, the core molding plate will be open to reveal the finished molded part with no runners attached.
There are two categories of hot runner systems, those that are heated externally and the ones that are heated internally. The external heating systems are best suited to sensitive polymers, while the internal heating systems grant better flow management. The procedure is regarded for being very efficient in eliminating the use of multiple runners. Recycling and regrind procedures will have no impact on cycle times. There is a separate system called “Insulated runner” that keeps the plastic in a molten state. This system is best suited to deal with semi-crystalline polymers that have low thermal conductivity.
Pros and Cons of Each System
You probably can tell by now that there are benefits to each procedure depending on the tasks they are needed for, but we can still call some differences between them to hammer the point home. Regarding cold runner systems, these are considered very cost-effective, especially when they are compared to the hot runner option. The overall cost to create a molded item and the low levels of maintenance are a great selling point. But both procedures are capable of handling diverse types of resins that the other can’t. Cold runners are pretty flexible when it comes to adapting upgrades, but they still have limitations when it comes to materials.
One of the most noticeable cons of cold runner systems is the production of the runner itself. When we work with two-plate cold runner systems, they have to be separated manually from the finished part after each run. There is also the fact that these runners have to be reground and recycled after each run cycle. This means losing a lot of material after the task is done. The removal of the sprues and runners also takes a lot of time, and it adds the time cycle time, translating in a slow production rate.
Hot runner systems have the best performance time-wise between the two. They can deliver a product in half the time than cold runner systems. By suppressing the runners, we don’t have to deal with any of the issues after the product is done. There is no sprue removal, and no regrinding and recycling needed. Lesser runners also take away any potential to waste material during the molding process. All these factors contribute to cost reduction and the increase in the productivity of the mold.