Plastic injection molding is a commonly used manufacturing process in fabricating plastic parts or products. There are many applications for this technique, and they vary greatly in sizes, materials, and complexity. When we say injection molding, it uses an injection molding machine, the plastic material, and the mold. In producing the parts, the plastic material is melted inside the machine and injected into the mold, where it cools and solidifies. But it is not as simple as that.
There are many essential things you have to learn about plastic injection molding. This article will help you understand the process, benefits, and applications of this vital manufacturing method. You will also get acquitted with some of the terms used in injection molding.
What is plastic injection molding?
Plastic injection molding is a manufacturing technique used in producing large quantities of products or parts. It is the go-to process for mass production that needs thousands, if not millions, of the same component from a mold.
It presents many advantages and at the top is its ability to produce products en masse. Another advantage is the cost of production. Because the output is in large quantities, the price per unit is meager, and the more parts are produced, the lower the price will be. There are many benefits that industries love about plastic injection molding. Here are some of them:
- It has low waste rates– Compared with conventional manufacturing methods like CNC machining, where there is a substantial amount of material is removed from the sheet or block to create a product. In plastic injection molding, the waste always comes from four areas: the location of the gates, the runners, the sprue, or sometimes from the cavity of the part.
- It is highly repeatable– Plastic injection molding can produce identical parts. This benefit is particularly critical when you need reliability and consistency.
Applications of Plastic Injection Molding
The most common use of plastic injection molding is in the production of thin-walled plastic parts, much like plastic housings. These products are mostly enclosures with many bosses and ribs on its interior. Some of the uses of these housings include products like household appliances, power tools, consumer electronics, and automotive dashboards.
You can also find them mostly in open containers like buckets. It is also widely used in everyday products like plastic toys and even your toothbrush. In the medical field, plastic injection molding produces syringes and valves.
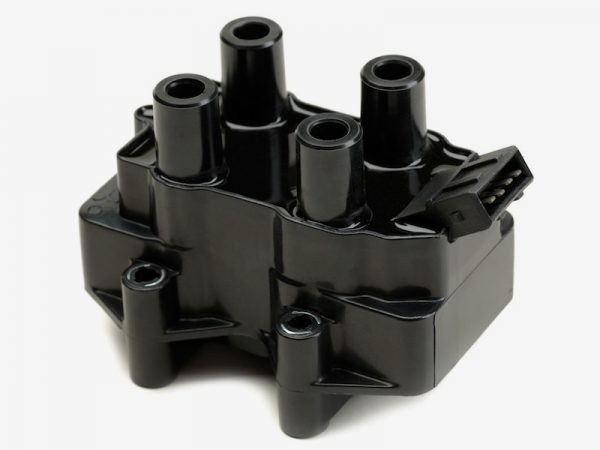
plastic injection molding products*
plastic injection molding products is from https://www.hansemold.de/
Its Processes
The plastic injection molding process is concise, it takes only about two and a half minutes. But did you know that there are four stages involved?
Here are the stages in this production process:
- Clamping– Before injecting the material into the mold. The two halves of the pattern are placed securely in the clamping unit. Both halves are attached in the machine, with the other half in the sliding position. What the device does is push the halves together before injecting the material.
- Injection – The raw material in the pellet form is fed into the injection molding machine. In this stage, this material is melted by pressure and heat. It is this molten plastic that is injected into the mold very quickly. There is a specific calculation for the material to have an accurate shot at the mold along with the injection time and pressure.
- Cooling– Inside the mold, the molten plastic will start to cool as soon as it touches the interior surfaces of the mold. When this plastic material cools down, it will take the shape of the mold. During this stage, the mold is not allowed to be opened until the cooling tape is finished.
- Ejection– When the cooling time has elapsed, the cooled part will be ejected from the mold using a unique ejection system that is attached at the bottom of the mold. The finished part slides out of the mold by force or using a mold release agent.
After the plastic injection molding cycle, there are some post-processing employed like trimming the excess material and any flash using cutters.
For thermoplastics, the waste materials and trimmings can be recycled using a plastic grinder. It converted the material into pellets and reused in the injection molding activity.
The Downsides of Using Plastic Injection Molding
One of the downsides of plastic injection molding is the higher upfront cost. This is due to the cost of designing, tooling, and designing the product. Because you are producing en masse, you need to make sure that there is no flaw in the products. It starts with getting the design right from the beginning.
Although it may sound easy, it is more complicated than you think. Having the right design involves lots of processes. It includes designing and prototyping, then developing the mold for the initial production, and refining the mold tool before the mass production.