Scroll down your Facebook feed, and it’s very likely you will find a story or a recommended piece of content related to the way plastic parts are becoming common ground for all types of prosthetics by replacing the metal components of these manufactured pieces. This is happening as fast as you read this every single day, simply because polymers and plastic have proven to be way more versatile and cheap to create them with time.
The film Battle Angel Alita inspired one of the most recent cases. A company named Open Bionics made a unique set of bionic arms entirely manufactured with plastic injection molding techniques for a young fan of the film named Tilly who lost both hands to a severe case of meningitis when she was only a year and three months old. What could have been a publicized story using expensive appendages turned out to be a ray of hope for many people when the company announced the overall costs of these new limbs.
Most of these appendages had been used plastic for a long time now, but they were always rigid, heavy and they only served the purpose of sitting still in the stump of the person receiving the appendage, making it really hard to manipulate. The new procedures to handle plastic have made it possible for more malleable components to be included in the creation of this prosthesis. Add on top of that the advances done to include sensors that perceive the impulses of the nerves in the arm of the user and you have a winning combination to make life easier for many of these person.
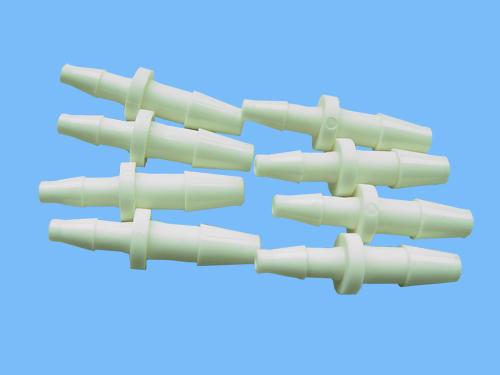
medical device components*
medical device components is from http://www.abspi.com
The Versatility of Plastics
Plastic is not exclusive to prosthesis these days. Almost all the tools or equipment used in medical facilities has been manufactured with metals exclusively for many years. The main reason behind it is because metals are easier to clean, and they have been deemed exceptionally efficient for emergencies and operating rooms. A lot of third world nations don’t have that option since they still face challenges when it comes to getting access to these tools for many reasons, but cheaper and safer options made of highly efficient polymers are used instead to create incredibly functional facsimiles to achieve the same goal.
Plastic Leads to Innovation
One of the greatest successes of plastic polymers in the medical industry is the work done by biomedical engineers with high-end polymers to create new forms of pacemakers that are lighter in weight and twice as functionals regular ones. There are also ongoing procedures to replace parts such as artificial joints, as well as growth-inducing medical implants. One of the best reasons for this course of actions is that a lot of polycarbonates, as well as quite a few biopolymers, are not rejected by the human body at all. They also reduce the time of recovery and are a lot cheaper than their metal counterparts.
Plastic Polymers Saves Money
The closing idea of our previous item is the main topic of discussion here. Polymers used to make plastic parts for medical devices can be reused and recycled. The lowered manufacturing cost takes place because many of these raw materials are very affordable and make the use of plastic a cost-effective procedure. Plastic injection molding is the way of the future because it has made the creation of these medical parts easier, with a single structure to be created that begins with the choice of the best resin and the use of computer designs to create a working prototype.
Plastic Leads to Enhanced Safety
Plastic is the best medicine for people with a phobia to germs. The food industry and the medical industry use a lot of antimicrobial plastics, to increase the safety of their products and to prevent infections. The materials used repel bacteria on a lot of surfaces that are commonly touched by hospital staff and other patients. There is also the fact that some patients are sensitive to metals, so they need plastic utensils to accommodate them. Let’s also remind that some of the most common parts replaced on surgeries such as hips use plastic parts now. Plastics are also lighter in weight and can help a patient get accustomed to their new prosthesis faster. A quick search online will reveal how at least any hospital now have at least 80% of all their tools made using plastic polymers.
Closing Thoughts
The increasing use of plastics will be ongoing for years to come because they are great to avoid spreading infections. Plastic is also very practical for design purposes, and it’s the way to go to make small parts easier and with diverse complexion and colors. Polymers might not be as strong as metal, but they have proven to be durable and resistant when it comes to organic interaction.