In the production and manufacturing sector, rapid tooling is also known as prototype tooling that is used in both prototypes or soft mold tooling. The entire tooling technique uses injection molding to produce parts/ products ins a faster and economical way.
In much simpler terms, rapid tooling is used when it comes to the fabrication of prototypes before they are released onto the mass-market. Aside from cheap production and affordable prices, the technique also allows for testing and validation of the final products before you can pour all of your money into the project.
Rapid tooling uses high-quality grade raw-materials providing you with a clear picture of how the parts and products will be used in real-life applications. This also allows for testing the materials chosen ensuring that it’s the right fit for the projects.
In this post, we will be discussing some key uses of rapid tooling techniques:
Opening up door and opportunities for innovation
One of the key benefits that come with rapid tooling is opening up new doors for innovation and invention allowing designers and engineers to explore their creativity without limitations. It does so by removing the disadvantages and limitations that come with conventional tooling.
Traditional prototyping entails the creation of the tooling prototype and the physical segments making the entire process quite tedious and leaves less room for innovation.
Incorporating rapid prototyping in the manufacturing process will enable the originators to create models that will fuse complex and intricate shapes that would have been otherwise impossible with basic tooling techniques.
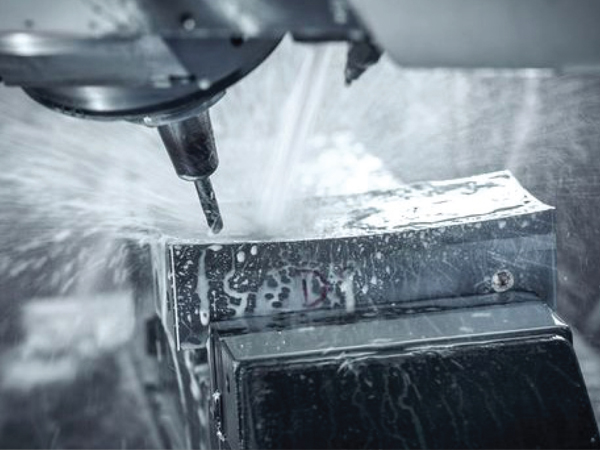
Rapid tooling*
rapid tooling is from wcm.com
Efficiency and effectiveness
Rapid tooling will significantly reduce the time required to make unique and exclusive devices and molds needed during demonstration and testing. As a result of rapid tooling, the time between the creation of the product and the examination manufacturers will be able to save a lot of time and money.
The results of this tooling technique will be the creation of identical models that can be easily used for execution, structure, testing highlights, and the ease of use. Because the whole process is automated, designers can quickly point out and fix design flaws on the prototype thus improving its efficiency.
Rapid tooling will give both manufacturers and clients an edge over their rivals by ensuring their products/parts hit the market on time. Your competitors will have no option but to improve proficiency and speed.
Cost-effective
Another advantage of rapid tooling is the cash-saving feature, parts and products are formed using an additive process thus allowing for testing as well as stress. Engineers can test for blemishes and point out the weak parts to be rectified before mass-production is rolled out saving you a lot of money in the process.
There are plenty of reasons why you should choose rapid tooling, it’s a quick and model tooling procedure that will enable you to create parts and products in a fast and simple manner compared to other forms of production currently on the market.
The fact that it allows market testing makes it perfect for low-production runs making it ideal to take your business to the next stage as it will cater to your individual needs and preference.